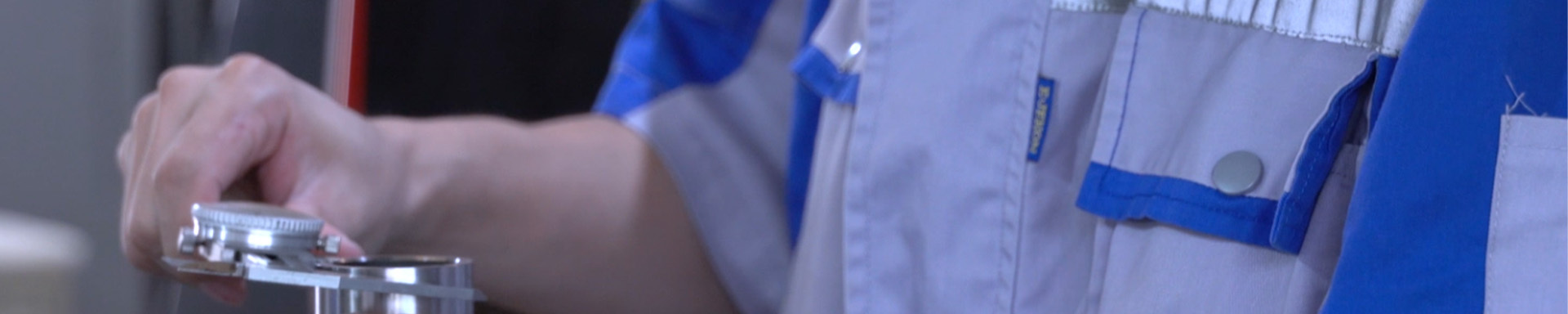
Vos environnements d’exploitation sont-ils adaptés aux alliages de cobalt ?
2025-02-13 09:00Caractéristiques de base et conditions de travail applicables des alliages à base de cobalt
1. Avantages en termes de performances dans des environnements extrêmes
Les alliages à base de cobalt (à base de cobalt, contenant du chrome, du tungstène, du molybdène et d'autres éléments) sont particulièrement remarquables dans les scénarios suivants :
Résistance à l'usure à haute température : il peut maintenir une dureté élevée et une résistance à l'usure supérieure à 800 °C et convient aux aubes de turbine à gaz, aux surfaces d'étanchéité de soupapes à haute température, etc.
Résistance à la corrosion et à l'oxydation : Dans les milieux acides ou les environnements de métaux en fusion (tels que le zinc et le plomb), la résistance à la corrosion est meilleure que celle des alliages à base de nickel, tels que les pompes et vannes chimiques, les rouleaux de galvanoplastie, etc.
Résistance à la fatigue thermique : Convient aux pièces soumises à des cycles thermiques fréquents, comme le revêtement de la chambre de combustion des moteurs d'avion.
2. Analyse des scénarios d'application typiques
Industrie énergétique et chimique : manchons à rouleaux creux, vis de machines de moulage par injection, vannes haute température et haute pression, etc., qui nécessitent à la fois une résistance à l'usure et à la corrosion.
Aéronautique : pièces à haute température et haute résistance telles que des aubes directrices de turbine et des composants de chambre de combustion.
Dans les industries médicales et spéciales, des alliages biocompatibles (tels que ASTM F75) sont utilisés pour les articulations artificielles, et des alliages à haute dureté (tels que W-21 avec HRC58) sont utilisés dans les environnements d'usure difficiles.
Solutions alternatives et guide de sélection de marques
Pour éviter les restrictions de marque, les marques générales suivantes ou des matériaux similaires peuvent être sélectionnés :
1. Marques internationales standard
Les séries cobalt-chrome-tungstène, telles que UNS R30006 et R30021, conviennent aux pièces résistantes à l'usure à haute température.
La série cobalt-chrome-molybdène, telle que UNS R30021, convient aux pompes, vannes et dispositifs biomédicaux dans des environnements acides.
2. Équivalences nationales
Les alliages haute température de la série GH, tels que GH5188 (correspondant à Haynes 188) et GH5605 (correspondant à L605), répondent aux exigences haute température des domaines de l'aviation et de l'énergie.
Les matériaux personnalisés, tels que l'alliage W-21 (HRC58) de Shanghai Rongkun Metal, peuvent remplacer les alliages traditionnels à base de cobalt à haute teneur en carbone pour la protection contre la corrosion du métal en fusion.
3. Compatibilité des processus
Technologie de formage : la métallurgie des poudres, le moulage de précision, le forgeage et d'autres procédés peuvent s'adapter à différentes exigences morphologiques (telles que les fils ultrafins et les moulages de précision).
Soudage et réparation : Le fil de soudage à base de cobalt (tel que AWS A5.21 ErCoCr) pour le surfaçage peut réparer efficacement les pièces usées.
Considérations clés pour le choix des matériaux
Équilibre entre coût et performance : Les ressources en cobalt sont rares. Il est recommandé de privilégier les alliages à base de nickel ou de fer (comme l'Inconel 718) pour répondre aux exigences de température moyenne grâce à l'analyse des conditions de travail et d'utiliser des matériaux à base de cobalt uniquement dans des conditions extrêmes.
Tests et certifications par des tiers : assurez-vous que le matériau répond aux normes telles que ASTM B462, GB/T 14992 et est vérifié par des institutions faisant autorité (telles que le National Iron and Steel Materials Testing Center).
Efficacité de la chaîne d’approvisionnement : sélectionnez des fournisseurs disposant de stocks de produits semi-finis (comme une livraison dans les deux semaines) pour raccourcir les cycles de production.
Étude de cas industrielle : solution alternative réussie
Une entreprise chimique utilise l'alliage UNS R30006 pour fabriquer des surfaces d'étanchéité de vannes haute température. Après avoir remplacé l'alliage à base de nickel d'origine, la durée de vie est multipliée par 3, tandis qu'il peut résister à des milieux corrosifs avec un pH de 2 à 12, et le coût de maintenance annuel est réduit de 40 %.
Les alliages haute température à base de cobalt sont le matériau de choix dans des conditions de travail complexes, mais des nuances et des procédés alternatifs doivent être sélectionnés en fonction des besoins spécifiques. Il est recommandé aux utilisateurs de travailler avec des fournisseurs de matériaux et des organismes de test pour effectuer des analyses de sélection de matériaux personnalisées afin de maximiser les avantages économiques et la fiabilité des équipements.