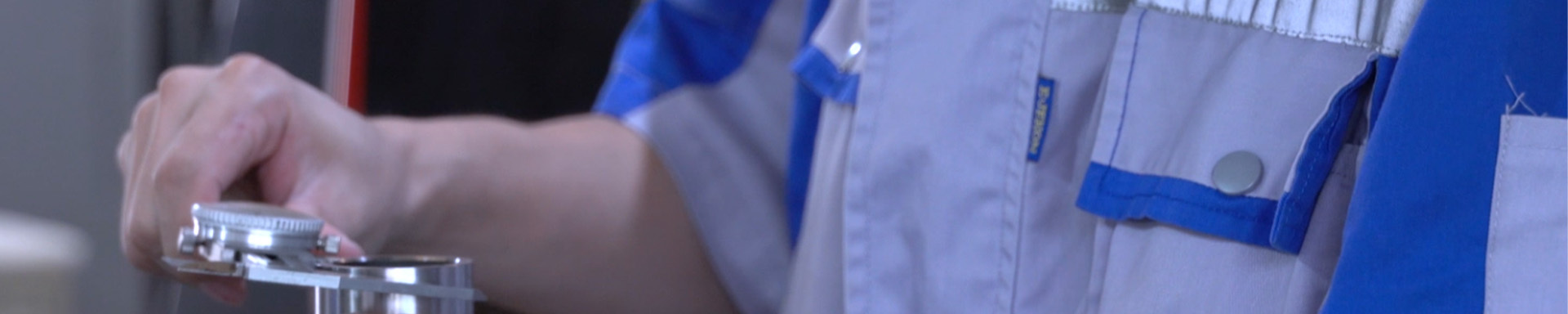
Application de l'alliage de cobalt dans un environnement à très basse température
2025-07-04 09:00Dans le domaine de l'ingénierie des ultra-basses températures, les matériaux des accessoires d'équipement doivent présenter une stabilité mécanique, une résistance à la fragilisation et une résistance à la corrosion à des températures extrêmes. Les alliages à base de cobalt offrent d'excellentes performances globales dans les environnements ultra-basses températures grâce à leur composition et leur microstructure uniques. Ils sont devenus des matériaux clés pour les pièces détachées dans l'aéronautique, le GNL, la technologie supraconductrice et d'autres secteurs.
Alliages de cobalt
Les alliages de cobalt sont à base de cobalt, auquel sont ajoutés principalement du chrome, du tungstène, du carbone et d'autres éléments. La structure cristalline hexagonale compacte du cobalt offre une excellente ténacité à basse température, et le Cr dense2LE3Le film d'oxyde résiste efficacement à la corrosion. Le tungstène améliore la résistance de la matrice grâce au renforcement de la solution solide, tandis que le carbone forme des carbures de haute dureté avec le chrome et le tungstène, uniformément répartis dans la solution solide à base de cobalt pour former une structure squelettique extrêmement dure, offrant à la fois résistance à l'usure et ténacité. Cette structure de phase complexe le rend moins sujet à la fragilisation à très basse température et lui confère une excellente résistance aux chocs.
L'avantage principal des alliages de cobalt dans les environnements à très basse température
Les alliages de cobalt conservent une résistance et une plasticité élevées à -196 °C, et la ténacité à basse température de leur solution solide à base de cobalt inhibe efficacement la propagation des fissures. En revanche, l'acier inoxydable ordinaire est sujet à la fragilisation due à la transformation martensitique à très basse température. Parallèlement, l'alliage de cobalt évite les changements de phase de la structure cristalline grâce à l'optimisation de sa composition et assure la stabilité structurelle.
Dans les milieux à très basse température comme le GNL, le revêtement de surface en alliage de cobalt résiste aux environnements corrosifs contenant du Cl⁻. Par exemple, une vanne papillon GNL utilise un corps de vanne à revêtement en alliage de cobalt, associé à un procédé de traitement cryogénique, de sorte que la structure flottante bidirectionnelle de la bague d'étanchéité assure une étanchéité radiale équilibrée, réduisant ainsi considérablement l'usure et prolongeant la durée de vie.
Le carbure haute dureté de l'alliage de cobalt résiste efficacement à l'usure par abrasion et à l'érosion à très basses températures. Par exemple, dans les manchons et les bagues d'étanchéité des pompes GNL, la résistance à l'usure de l'alliage de cobalt prolonge sa durée de vie de 3 à 5 fois celle des matériaux ordinaires. De plus, sa résistance à la fatigue lui permet de supporter des cycles de température fréquents.
Application de l'alliage de cobalt dans le domaine des températures ultra-basses
Équipement de gaz naturel liquéfié (GNL)
Grâce à sa faible température et à sa résistance à l'usure, l'alliage de cobalt est devenu un matériau idéal pour les surfaces d'étanchéité des vannes, les roues de pompes et les paliers des composants clés des réservoirs de stockage de GNL, des navires de transport et des pipelines de transport. Après traitement cryogénique, les composants d'étanchéité préparés répondent aux exigences strictes des conditions de fonctionnement à basse température, réduisent considérablement le couple d'ouverture et de fermeture des équipements et prolongent leur durée de vie, garantissant ainsi un fonctionnement sûr et stable de la chaîne industrielle du GNL.
Système de propulsion cryogénique spatial
L'alliage de cobalt joue un rôle essentiel dans les pompes de turbine, les soupapes et les composants de tuyauterie des moteurs-fusées à hydrogène/oxygène liquide. Face à des températures extrêmement basses (-253 °C), son excellente résistance à la cavitation et aux chocs thermiques garantit la fiabilité des composants centraux, tels que les aubes de turbine et les joints, sous des charges alternées à hautes et basses températures. Cet alliage offre à la fois une résistance à haute et basse température et une ténacité optimale, et s'adapte aux conditions thermomécaniques complexes du système de propulsion.
Technologie supraconductrice et ingénierie cryogénique
Les alliages de cobalt sont devenus le matériau privilégié pour les structures de support et les composants de connexion grâce à leur faible coefficient de dilatation thermique dans la conception structurelle des aimants supraconducteurs et des équipements de réfrigération cryogénique. Cette caractéristique leur confère une bonne compatibilité thermique avec les matériaux supraconducteurs, réduisant ainsi efficacement l'impact des contraintes thermiques dans les environnements à basse température. Même à des températures extrêmement basses (-269 °C), leurs propriétés mécaniques stables garantissent la fiabilité et l'intégrité de la structure de l'équipement.
Analyse comparative des propriétés des matériaux
D'après les performances comparatives, les alliages de cobalt présentent d'excellentes performances en termes de dureté, de ténacité à basse température, de résistance à la corrosion et à l'usure. Leur dureté à température ambiante peut atteindre 40 à 60 HRC, soit une valeur nettement supérieure à celle des alliages de titane et de l'acier inoxydable.
En ce qui concerne la ténacité à basse température, les alliages de cobalt ne présentent aucun phénomène de fragilisation à -196℃, les alliages de titane peuvent conserver une certaine plasticité à -253℃ et l'acier inoxydable ordinaire est sujet à une rupture fragile à -196℃.
Les alliages de cobalt ont une excellente résistance à la corrosion Cl⁻, les alliages de titane ont une bonne résistance aux milieux oxydants et l'acier inoxydable doit être passivé pour améliorer la résistance à la corrosion.
En ce qui concerne la résistance à l'usure, les alliages de cobalt ont d'excellentes performances grâce au renforcement du carbure, les alliages de titane ont une résistance à l'usure modérée et reposent sur un traitement de surface, et l'acier inoxydable a une faible résistance à l'usure et est sujet à des problèmes d'usure pendant l'utilisation.