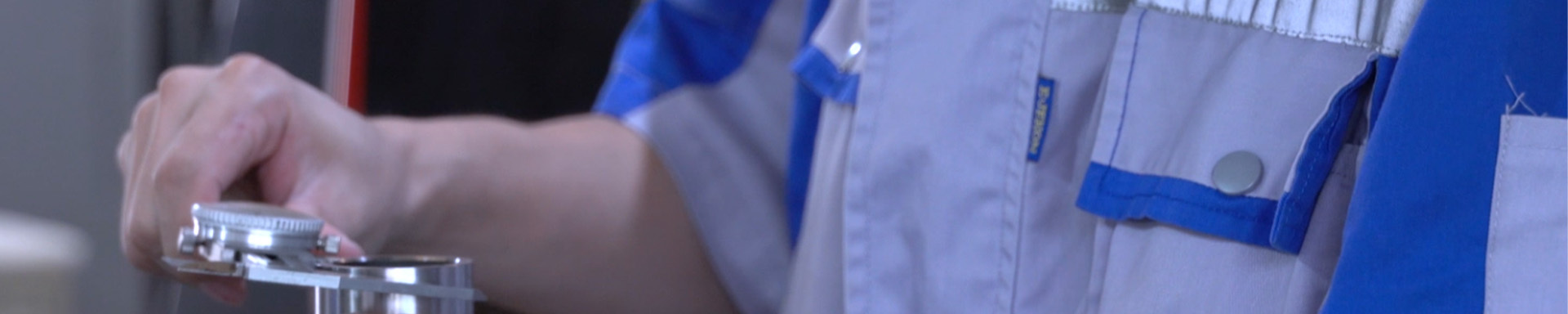
Carbure de tungstène et alliage de cobalt
2024-11-21 09:00Le carbure de tungstène (WC) est un matériau composite fabriqué à partir de tungstène et de carbone grâce à un procédé spécifique. Il est largement apprécié pour sa dureté et sa résistance à l'usure extrêmement élevées. Il a un point de fusion élevé de 2870°C, ce qui lui permet de maintenir d'excellentes performances même dans des environnements à haute température. Le carbure de tungstène est largement utilisé dans la fabrication de pièces qui nécessitent une excellente résistance à l'usure et aux chocs, telles que les couteaux, les matrices, les poinçons et les abrasifs.
Les alliages de cobalt sont des matériaux d'alliage composés de cobalt et d'autres éléments d'alliage tels que le chrome, le nickel, etc. Ils présentent généralement une bonne résistance à l'usure, à la corrosion et une bonne stabilité à haute température. Les alliages de cobalt fonctionnent bien dans les environnements à haute température et corrosifs, ce qui en fait le matériau privilégié pour les industries telles que l'aérospatiale, la production d'énergie et les produits chimiques.
Résistance à l'usure
En termes de résistance à l'usure, le carbure de tungstène se distingue par sa dureté extrêmement élevée, ce qui en fait un choix idéal pour la fabrication de pièces de rechange résistantes à l'usure telles que les sièges de soupape, les roulements et les pointes de scie. Cependant, les alliages de cobalt excellent également en termes de résistance à l'usure, en particulier dans les applications qui doivent résister à des températures élevées ou à des environnements corrosifs. La résistance à l'usure des alliages de cobalt est principalement due à leur composition et à leur microstructure, ce qui leur permet de maintenir une longue durée de vie dans des conditions difficiles. C'est également un choix courant pour les pièces de rechange résistantes à l'usure.
Résistance à haute température
Les alliages de cobalt peuvent conserver de bonnes performances à haute température, ce qui constitue un avantage significatif par rapport au carbure de tungstène. Dans les environnements à haute température, le carbure de tungstène peut se dégrader en raison de la dilatation thermique et de l'oxydation. Les alliages de cobalt peuvent conserver une résistance et une ténacité élevées, ainsi qu'une bonne résistance à la corrosion, ce qui les rend largement utilisés dans les environnements à haute température tels que les turbines et les moteurs.
Coût
En raison du processus de fabrication complexe et du coût élevé des matériaux, les alliages de cobalt sont généralement plus chers que le carbure de tungstène. Cependant, dans certaines applications, les hautes performances et la grande fiabilité des alliages de cobalt peuvent les rendre plus rentables. Les entreprises doivent choisir le matériau le plus adapté en fonction de leurs besoins d'application, de leur budget et de leurs exigences de performance.
Lequel choisir pour votre application ?
Le choix entre le carbure de tungstène et l'alliage de cobalt dépend des exigences spécifiques de l'application. Pour les applications impliquant une usure ou une coupe importante, le carbure de tungstène est un meilleur choix en raison de son excellente dureté et de sa résistance à l'usure. Cependant, pour les applications qui nécessitent une stabilité à haute température, une résistance à la corrosion ou des performances complètes, les alliages de cobalt offrent d'excellentes performances. Lors de la sélection des matériaux, les entreprises doivent tenir pleinement compte de facteurs tels que leur environnement d'application, leurs exigences de performance et leur coût.
Le carbure de tungstène et les alliages de cobalt présentent tous deux des avantages uniques pour les applications industrielles. La compréhension des propriétés de ces matériaux garantit des performances et une rentabilité optimales. Si vous ne savez pas quel matériau convient le mieux à vos besoins, consultez un ingénieur ou un fournisseur de matériaux professionnel pour obtenir des conseils personnalisés.