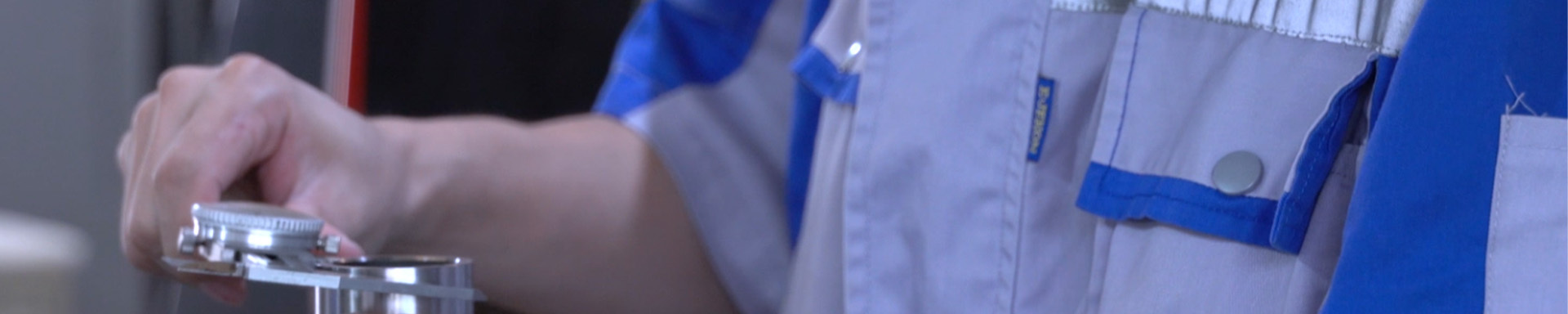
Utilisation des alliages de cobalt dans les extrudeuses à vis
2025-04-23 09:00Alors que l'industrie de la plasturgie exige de plus en plus de productivité, de durabilité des équipements et de respect de l'environnement, le choix des matériaux pour les vis et les fourreaux des extrudeuses est devenu un enjeu majeur de l'optimisation technologique. Parmi les nombreux matériaux hautes performances, les alliages de cobalt s'imposent progressivement comme le choix idéal pour les composants clés des extrudeuses plastiques, grâce à leur excellente résistance à l'usure, à la corrosion et à la température.
Caractéristiques techniques des alliages de cobalt
L'alliage de cobalt est un type d'alliage métallique dont les principaux composants sont le cobalt, le chrome et le tungstène, qui présente les propriétés fondamentales suivantes :
1. Résistance à l'abrasion supérieure : sa dureté peut atteindre HRC 50-65, ce qui est bien supérieur à celui de l'acier à outils ordinaire, et il peut réduire considérablement le taux d'abrasion de la vis et du canon dans la rotation à grande vitesse et le frottement du matériau.
2. Résistance aux hautes températures : dans un environnement à haute température supérieur à 500 °C, il peut maintenir la stabilité structurelle, pour éviter la déformation causée par la dilatation thermique.
3. Résistance chimique : excellente résistance aux additifs plastiques acides (tels que les ions chlorure dans le traitement du PVC) et à la corrosion par fusion à haute température.
4. Autolubrifiant : le film d'oxyde formé à la surface de l'alliage réduit le frottement direct métal sur métal, réduisant ainsi la consommation d'énergie et l'accumulation de chaleur.
Ces propriétés rendent les alliages de cobalt particulièrement adaptés aux scénarios d'extrusion à forte charge et à forte usure, tels que le traitement des plastiques renforcés de fibres de verre, des plastiques techniques (par exemple, PA, PEEK) ou des matériaux recyclés contenant des charges.
Alliages de cobalt dans les vis et les barils
1. Fabrication intégrale
Pour les petites extrudeuses ou celles n'ayant pas d'exigences de performances particulièrement élevées, il est possible d'utiliser une approche de fabrication intégrale, où les vis et les cylindres sont fabriqués directement à partir d'alliages de cobalt. Cette méthode présente l'avantage d'être simple et de se fabriquer relativement facilement, mais son coût est plus élevé.
2. Revêtement de surface
Pour les extrudeuses de grande taille ou plus sensibles aux coûts, un revêtement de surface peut être utilisé : la vis et le fourreau en acier ordinaire sont pulvérisés ou recouverts d'une couche d'alliage de cobalt. Cette approche présente l'avantage d'être moins coûteuse et d'améliorer efficacement la résistance à l'usure et à la corrosion de la vis et du fourreau. Les procédés de revêtement de surface les plus couramment utilisés sont la projection plasma, la projection à la flamme et le revêtement laser.
3. Structure de l'ensemble
Dans certains cas particuliers, il est possible d'utiliser, pour la structure de l'ensemble, un alliage de cobalt pour manchon intégré dans un cylindre en acier ordinaire, ou un alliage de cobalt pour mandrin à vis et chemise à vis en acier ordinaire combinés. Cette approche présente l'avantage de permettre de choisir la combinaison de matériaux la plus adaptée aux besoins, de réduire les coûts et de garantir la performance des pièces clés.
Analyse de la valeur économique : les avantages à long terme des alliages de cobalt dépassent largement les coûts initiaux
Bien que le coût initial des matériaux des alliages de cobalt soit plus élevé que celui de l'acier conventionnel, la valeur économique globale se reflète dans :
Réduction des pertes dues aux temps d'arrêt : la réduction des temps d'arrêt imprévus dus à des dommages aux vis ou au canon améliore l'utilisation de l'équipement.
Cycles de remplacement prolongés : les pièces renforcées en alliage durent plusieurs fois plus longtemps que les matériaux conventionnels, ce qui réduit considérablement la fréquence d'achat des pièces de rechange.
Amélioration de la qualité du produit : la précision dimensionnelle stable et la finition de surface réduisent le taux de rebut.