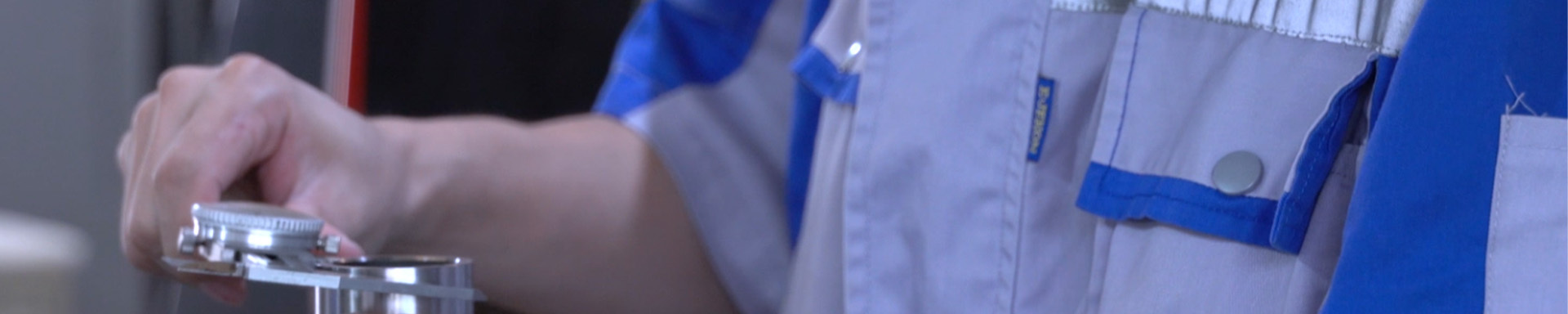
Comment choisir les bons matériaux pour les filières d’extrusion à chaud en continu pour le cuivre ?
2025-07-17 09:00Dans l'industrie de transformation du cuivre, l'extrusion continue à chaud est une technologie essentielle pour la production de profilés critiques tels que les barres et les fils de cuivre. Le choix des matériaux des matrices a un impact direct sur l'efficacité de la production, la qualité des produits et les coûts globaux. Cet article analyse les limites des aciers pour moules traditionnels au regard des besoins réels de production, détaille les avantages des alliages de cobalt et fournit des conseils professionnels aux entreprises pour le choix des matériaux des matrices d'extrusion continue à chaud du cuivre, à travers des cas d'application.
Définition des exigences matérielles pour l'extrusion continue à chaud du cuivre
Exigences de base pour les matrices dans l'industrie
Les barres et fils de cuivre sont largement utilisés dans la transmission d'énergie, le transport ferroviaire, les appareils électroniques et d'autres domaines. Leur production repose sur le fonctionnement efficace de machines d'extrusion à chaud horizontales continues. Ces machines transforment les billettes de cuivre en profilés de sections spécifiques grâce à un processus d'extrusion ininterrompu, ce qui impose des exigences extrêmement élevées en matière de stabilité des moules, de résistance à l'usure et de capacité de rétention de précision. Les moules doivent maintenir des performances constantes sur de longues périodes de production pour garantir des spécifications de produit uniformes.
Défis dans l'environnement d'exploitation du moule
L'environnement d'exploitation pour l'extrusion à chaud continue de cuivre est extrêmement rigoureux : les moules doivent résister en permanence à des températures de 500 à 600 °C, à des pressions d'extrusion de plusieurs centaines de mégapascals et à d'importantes frictions dues à l'écoulement du cuivre. Dans ces conditions, la dureté à haute température, la résistance à l'usure et à la fatigue thermique du moule deviennent les principaux critères d'évaluation de ses performances. Toute déficience de ces propriétés peut entraîner des interruptions de production ou des rebuts.
Inconvénients des aciers à moules traditionnels
Défauts de performance des aciers H11, H13 et H21
Les aciers pour moules à chaud H11, H13 et H21 sont depuis longtemps couramment utilisés pour l'extrusion du cuivre. Cependant, l'extrusion à chaud continue entraîne une décarburation importante à haute température. Au-delà de 500 °C, les éléments carbonés présents à la surface de l'acier s'oxydent et se perdent facilement, ce qui diminue rapidement la dureté superficielle et accélère l'usure du moule. Au-delà de 600 °C, la dureté de ces aciers chute brutalement, les rendant incapables de maintenir la résistance structurelle requise pour l'extrusion, ce qui affecte directement la précision dimensionnelle du cuivre. Les cycles fréquents de chauffage-refroidissement induisent des contraintes alternées dans le moule, entraînant la formation de microfissures qui se propagent progressivement et finissent par provoquer une défaillance prématurée du moule.
Pourquoi l’alliage de cobalt est-il le choix privilégié pour les moules d’extrusion à chaud en cuivre ?
Avantages des propriétés matérielles
L'alliage ST 3, représentatif des alliages à base de cobalt, présente d'excellentes caractéristiques de résistance mécanique et de ténacité, de résistance aux températures élevées et de résistance à la corrosion, ce qui le rend particulièrement adapté aux conditions difficiles de l'extrusion à chaud continue des matériaux en cuivre. À des températures supérieures à 600 °C, l'alliage ST 3 conserve une dureté de 40 à 45 HRC, diminuant progressivement avec la température, évitant ainsi une chute brutale et garantissant une stabilité structurelle dans des conditions de températures élevées prolongées. Sa résistance à l'usure provient du renforcement du composé intermétallique inhérent à l'alliage plutôt que des carbures. De ce fait, sa résistance à l'usure par frottement à haute température est 3 à 5 fois supérieure à celle de l'acier H13, ce qui lui permet de résister efficacement à l'usure superficielle causée par l'écoulement du cuivre. Les alliages à base de cobalt supportent de fréquentes variations de température, réduisant ainsi l'apparition de fissures dues aux contraintes thermiques et prolongeant considérablement la durée de vie du moule.
Étude de cas client indien
Une entreprise indienne de transformation du cuivre était initialement préoccupée par le coût élevé de l'alliage ST3 lors du choix des matériaux de moulage. Nous avons constitué une équipe dédiée pour intervenir dans le processus de conception du moule : grâce à la modélisation 3D, nous avons optimisé la structure du canal d'alimentation, réduit l'épaisseur du matériau dans les zones de travail centrales et adopté un procédé combinant ST3 et H13 pour l'assemblage à chaud, réduisant ainsi l'utilisation d'alliage de cobalt tout en préservant la résistance.
Après avoir testé le moule optimisé en alliage ST 3, le client a constaté une amélioration significative de l'efficacité de sa production. Malgré une augmentation du coût par moule, l'entreprise a réalisé des économies globales.
Sélection du bon matériau de moule pour améliorer l'efficacité de la production de cuivre
La production efficace de cuivre par extrusion à chaud continue repose sur des matériaux de moulage hautes performances. Les limites de performance des aciers de moulage traditionnels dans les environnements à haute température et à forte usure constituent un frein au développement industriel. Les alliages de cobalt offrent une solution idéale à ce défi grâce à leur excellente dureté à chaud, leur résistance à l'usure et à la fatigue thermique.
Si vous rencontrez des problèmes tels qu'une durée de vie courte du moule ou une production instable, veuillez nous contacter pour une solution personnalisée.